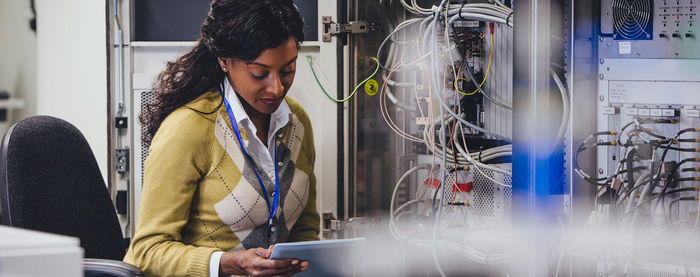
Funder
U.S. Department of Labor’s Employment and Training Administration
August 15, 2020
U.S. Department of Labor’s Employment and Training Administration
October 2015 – September 2020
Advanced Manufacturing
California, Colorado, Florida, Idaho, Illinois, Indiana, Kentucky, Michigan, Minnesota, Missouri, North Dakota, New York, Ohio, Pennsylvania, South Carolina, Washington, and Wisconsin
Chicago Federation of Labor Workforce and Community Initiative, Keystone Development Partnership, Labor Institute for Training, Michigan Workforce Development Institute, Wisconsin Regional Training Partnership, Working for America Institute of the AFL-CIO
* Register 1,450 new apprentices, 40% from underrepresented populations * Establish 150 employer sponsors
In today’s advanced manufacturing economy, most production workers, including those on the front lines, need more than the basic skills that were sufficient for factory work in previous decades.
To meet strict quality and safety standards, modern manufacturers need workers with a good deal of expertise. But experienced employees are aging out of the labor market and new talent is scarce. Employers often have a hard time finding skilled young workers who can help grow this critical sector of the U.S. economy.
The Industrial Manufacturing Technician (IMT) Apprenticeship fulfills that demand for labor by helping employers and unions attract and train people to work in advanced manufacturing facilities.
A nationally recognized apprenticeship registered with the U.S. Department of Labor, the IMT is hybrid training program in which participants acquire knowledge and skills that are essential in advanced manufacturing environments. Workers who complete the 18-month or 3,000-hour apprenticeship will learn to do the following:
IMT graduates are prepared to work in settings as diverse as food processing plants, foundries, plastics production facilities, and biomedical plants.
Since 2015, JFF has enrolled 900 IMT apprentices at an average starting wage of $18.50 an hour. By the end of the 18-month apprenticeship, the average hourly wage increases to $25.
In 2020, a return on investment study of the IMT program showed that every dollar an employer sponsor invested in the program yielded a return of $1.48.
This study measures the business impact of the Industrial Manufacturing Technician Registered Apprenticeship program on six apprenticeship sponsors. Apprenticeships are drastically underutilized as a standard part of the development and training of the American workforce.…
Meeting the demand for a competitive 21st century manufacturing workforce will require training models that work. Apprenticeships are a powerful solution that equip workers with the technical skills needed to drive the country’s manufacturing industry…
An Illinois manufacturer uses the Industrial Manufacturing Technician apprenticeship program to build its workers’ skills. The Industrial Manufacturing Technician (IMT) apprenticeship program provides frontline manufacturing production workers with the knowledge and competencies needed in the…
Hayes has a long history as a manufacturer of motorcycle brakes, and it’s seeking to extend that expertise into other automotive markets. For Hayes to diversify successfully, its workers need to be flexible, nimble, and…
This profile highlights how KDP, a Pennsylvania intermediary, uses mentorship and group sponsorship to strengthen and develop the IMT. Intermediary Profile Keystone Development Pipeline (KDP) This workforce product was funded by a grant awarded by…
This profile highlights how WDI, a Michigan intermediary, expands the IMT apprenticeship program through building and maintaining close relationships with employers. Intermediary Profile Workforce Development Institute (WDI) This workforce product was funded by a grant…
With support from WRTP/ BIG STEP and JFF, manufacturing employers have transformed the skills of their workforce with apprenticeship programs like the Industrial Manufacturing Technician Registered Apprenticeship. “It’s all about self-growth. If a person is…
The AFL-CIO Working for America Institute, in partnership with the Wisconsin Regional Training Partnership/BIG STEP and JFF, developed the Industrial Manufacturing Technician Apprenticeship. Its impact is showcased in this profile of a participant in the…
As a result of his Industrial Manufacturing Technician apprenticeship, Rick Bostwick is moving up the career ladder at Dayton-Phoenix Group. In 2016, Rick Bostwick had been working on factory floors for more than 10 years…
On the Path to Advancement: A Journey Back To School Through Apprenticeship The 18-month IMT apprenticeship trains frontline manufacturing workers to set up, operate, monitor, and control production equipment. Apprentices learn to understand manufacturing as…